Walking around Bellingham’s Fountain District, I happened upon WindWorks, a locally owned instrument repair shop specializing in the highest quality wind instrument, percussion and string repair. I spied in the window something that looked like a tangled mass of brass.
In fact, the object was a working piece of art made as a wedding gift for owners Ed and Kat DeVaney by Bellingham’s Jack Champagne, French Horn player, brass teacher and musical instrument builder. Jack designed this one-of-a-kind three-belled horn specifically to play “Here Comes the Bride.”
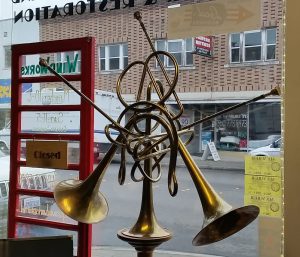
Jack picked up his first brass instrument, the trumpet, when he was ten years old while living in Taylor, Michigan. He moved to Whatcom County in the early 80s to attend school at Western Washington University. His classmates led by example and taught Jack that he needed to practice “a lot” to be a good musician. His dedication and passion for music has endured the decades, as he continues his almost daily morning practice routine. Jack is a regular member of both the Whatcom Symphony Orchestra and the Glacier Bay Brass Quintet. He also plays other gigs as requested.
Jack teaches all levels for all types of brass. “All of them, trumpet, french horn, trombone, tuba, euphonium,” he emphasizes. He usually starts beginners with the euphonium, as it’s the easiest to play and make a good sound. “If you can buzz a D, you can play a horn,” he says.
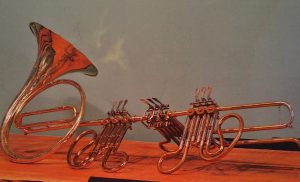
Enabling a student to make a good sound in under two minutes encourages them to continue. As they progress, they play other instruments. Jack introduces the trumpet last as it’s the most challenging and a frustrated student is no fun for anyone. Jack is fulfilled by watching an excited student getting a kick out of what they are able to do. He also has a “library” of usable instruments.
I recently spent some time in Jack’s Bellingham studio and workshop, looking at many finished sculpted works, the works in progress and the hundreds and thousands of pieces of brass that line the walls and fill the drawers in his shop.
I wanted to know why Jack (or anyone) would do what he does to perfectly good brass instruments. As it turns out, most of the materials he uses were never made into finished instruments in the first place. Instead, they were sitting in warehouses gathering dust. Other materials are repaired or repurposed. Jack admits he knows enough about brass instruments to repair everything on the horn except for the valves.
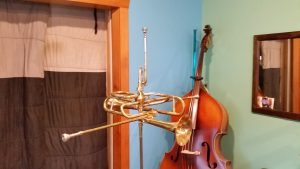
About three years ago, Jack sculpted his first multiple instrument. Multiple means there are at least two mouthpieces (places to buzz). “That first multiple chord was magic,” he says. He has been building multiple instruments ever since.
Jack found a few brass instrument manufacturing and re-furbishing plants in the midwest. He traveled to Elk Horn Wisconsin and met Craig Anderson. When Craig saw photos of Jack’s creations, Craig gave Jack a van full of brass instrument material.
Since then, Jack has developed relationships across the country with other current and former brass instrument manufacturers who sell and sometimes give him instrument components that aren’t patented and that they wouldn’t otherwise use. Jack will take just about everything they are willing to let go of that can fit in the back of his van. The manufacturers like that Jack is turning what would otherwise be landfill into creative and usable instruments.
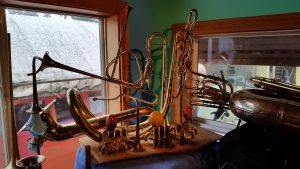
He’ll turn bells, tubes and valves into beautiful (and often odd-looking) working pieces of art. “All of them play,” he says proudly, although he admits that there is one creation that he has not quite figured out how to get a sound out of yet. Jack’s productions are special, one-of-a-kind and usually made with someone in mind.
Jack gifts the finished products away to acknowledge the recipient’s kindness. “I’m thankful that the recipients are willing to take it home,” he says. Sometimes, he admits, he doesn’t tell the recipient their instrument is ready, as Jack isn’t quite ready to say goodbye and let it go.
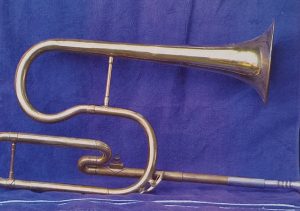
After more than 25 summers of working with participants of the Brass Chamber Music Workshop at Humboldt State, the sense of cooperation and kindness he observed there prompted him to embrace and spread kindness. “Make America Kind Again” will be a presence in the Jr. Ski to Sea parade this spring in Bellingham with T-shirts and silicone wristbands that say “Extra Special Kindness.”
I asked Jack what’s next for him. As he continues to work in his shop, he’s working towards a kinder society and, he said with a smile, “I’m doing what I want to do until I die.”